SumiRiko AVS Czech
How SumiRiko AVS Czech saved 80,000 EUR after implementing MES SoftLi
"In the first year of using MES SoftLi, our efficiency increased by 2.6%. In the second year, we achieved a 2% improvement in OEE. Every year, we save about 80,000 EUR. However, the system also has very positive psychological effects. Employees know that we understand what's really happening in production - and this awareness works wonders.“
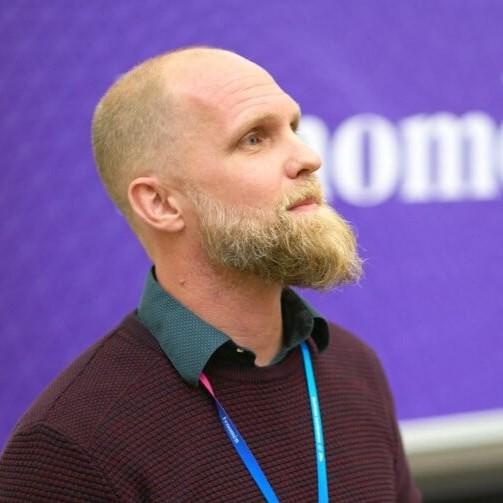
Ing. Jaroslav Ordelt,
Plant Operations Manager
About the client
SumiRiko AVS Czech is a South Moravian supplier of rubber components for the automotive sector. The company operates under the Sumitomo Riko Group – the global leader in automotive anti-vibration technology. Its client base includes major manufacturers such as Volkswagen, Audi, Škoda, BMW, Mercedes-Benz and Tesla or suppliers like Mubea and Thyssenkrupp.
The best-selling product at SumiRiko’s South Moravian plant in Drnovice has long been the silent block – engine mounts that suppress vibrations in vehicles.
But the company’s portfolio also includes mounts for exhausts, stabilizer bars, and radiators. SumiRiko additionally produces a range of niche items, such as vibration absorbers.
Its 360 employees work around the clock in three shifts.
They operate:
50 rubber injection molding machines
7 plastic injection molding machines
30 assembly lines
and 20 additional machines
SumiRiko takes pride in its high level of automation – a key factor that helps keep production costs low. That’s why so many companies choose to buy rubber products from them instead of from China or Mexico.
Before implementation: a struggle with the MES and with the vendor
SumiRiko was using a French MES, but it brought more frustration than benefits.
They had four major concerns with the system:
poor service – nothing could be customized to fit the customer's needs
weak data structure and difficult navigation
employees were reluctant to use the MES
inaccurate data
The IT guy had to do everything, which simply wasn’t effective. They were looking for a system that operators and production staff could use easily. With flexible functions that could be tailored to how they actually work.
It was a recurring issue.
SumiRiko, for example, had defined specific KPIs and management wanted to use them in MES reporting. But the MES system kept reporting based on factory defaults instead of Surimiko’s KPIs.
And there was no way to change it.
The turning point came when the company realized that MES was regularly providing inaccurate data.
This forced them to export everything to Excel and recalculate it.
To make things worse, they combined data from both the ERP and MES systems in Excel,
which only made navigation even more difficult.
Thus, every month, one employee had to spend two days just sorting and organizing the data.
"MES is meant to deliver the data you need immediately, not data that requires further recalculations in Excel,“ acknowledges now Jaroslav Ordelt, Plant Operations Manager.
Why they chose MES SoftLi?
SumiRiko conducted a market survey and were looking for a partner who:
is young and driven
develops his MES from scratch
doesn’t stick to old routines
strives for continuous progress
offers a fresh product at a reasonable price
seeks out what customers want and delivers it
doesn’t adopt the approach: “Here’s the product, take it or leave it”
gives SumiRiko the opportunity to influence the final form of the system
At least that’s how Jaroslav Ordelt explains his choice.
The key to successfully implementing MES system is its technical reliability
"The effect of implementing an MES system largely depends on how well it is integrated into your own structures, " says Ordelt.
The hardest part of implementing the MES system is convincing employees that it is a good thing that will make their work easier.
"With MES SoftLi, we started in the plastic injection department. The system immediately ran smoothly on the technical side, which is why the workers quickly got used to it," adds Ordelt.
His experience shows that it's difficult to implement something that people will later complain about, coming to you saying the data doesn’t match and that the whole thing is just unnecessary work.
That was the case with the previous supplier, but not with us.
The implementation faced several challenges
For example, data collection from vulcanizing presses.
"We have roughly 50 of them from 6 different manufacturers. Some are fairly old and only produce analog signals, so it was necessary to refine the data collection script to make it compatible with all machines. This took some time, but with SoftLi's help, we developed a script that solves this problem very reliably," recalls Ordelt.
MES SoftLi sheds light on the blind spots of analog systems
"After implementing MES SoftLi across most departments, we finally saw what was really happening in production – not just what people reported on paper. Those were often two completely different realities, especially during the night shift," adds Ordelt.
According to the Plant Operations Manager at SumiRiko, the blindness of analog systems lies in the fact that you don’t see the problems – so you don’t even realize they exist.
As Ordelt adds: " On paper everyone performs at 100 %, everything seems fine – but once you implement MES, you might learn that night shift workers were sleeping for an hour. That’s waste you’d otherwise miss."
Results of the implementation
Let’s start with the hard data perspective:
In the first year of using MES SoftLi, SumiRiko increased efficiency by 2.6%
In the second year, they achieved a 2% improvement in OEE
Each year, they saved approximately 80,000 EUR
Now from Jaroslav Ordelt's perspective: "It's great that we can see the data, analyze it, and take the right actions based on it. But MES SoftLi also has a very positive psychological effect. Employees know that we know what’s really happening in production. And that awareness works wonders," smiles the Plant Operations Manager.
He also appreciates the positive feedback from employees.
“Their reaction was better than I expected. We added the Andon module so that machine operators could request material delivery. The workers were genuinely happy – they said it was something they’d been missing for a while.”
“And honestly, we’ve needed this too. We don’t want handlers stocking machines with goods for three shifts in advance. And we also want visibility into how often handlers are called and how each one performs. Who knows – maybe five would be enough instead of the six we currently have,” notes Ordelt.
What SumiRiko no longer needs is the help of IT specialist whenever working with the MES system.
In MES SoftLi, anyone can adjust and format a report.
The supervisor can modify a production order during the shift.
People like the system and see its benefits for them as well.
“There’s nothing worse than analyzing bad data and making poor decisions as a result. That’s a waste of time. And time is money. With MES SoftLi, we no longer waste time. And we save around 2 million crowns per year,” recalls Ordelt.
Do you also want to increase efficiency and eliminate waste?
We help manufacturers of all sizes increase efficiency by up to 20%.
No paper. No downtime. No excuses.
We are the only ones offering a free and instantly available DEMO, as well as the option to test the system on your own machines, without any commitment.