Commercial foundry Turnov
How we increased the productivity of Commercial Foundry Turnov by 10% through the implementation of MES SoftLi
"The deployment of MES SoftLi took only a few hours, was completely smooth, and the results were evident within a few days. Thanks to clear production tracking, we improved the performance of individual workstations and enhanced their cooperation. This led to a 10% increase in overall productivity."
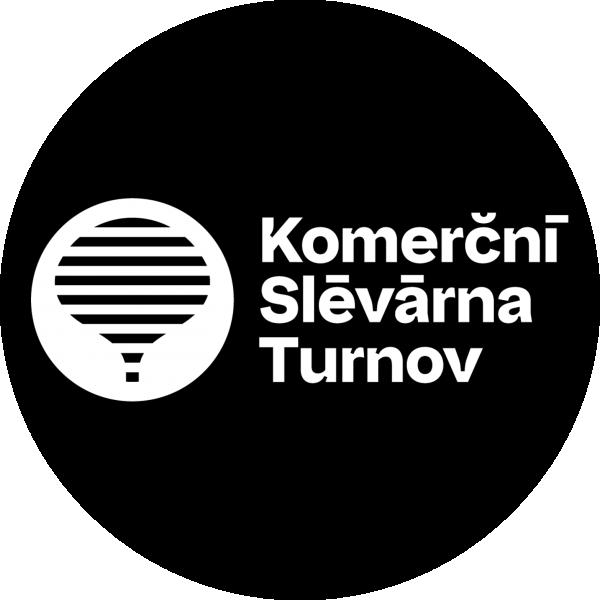
Ing. Pavel Světlík,
managing director
Commercial Foundry Turnov is a family-owned business that was established in 1997 by transforming the state-owned enterprise Sklostroj. For over 100 customers from the fields of engineering, energy, food industry, and transportation, it produces castings made of aluminum and gray, ductile and special cast iron.
The foundry utilizes 3 technological processes for casting production:
Molding line (high-volume production of smaller parts) – batch size: 20–1,000 pcs
Machine molding (low-volume production of larger parts) – batch size: 10–100 pcs
Hand molding (custom production of samples and prototypes) – batch size: 1–20 pcs
This allows it to cover a wide range of needs for its clients in the Czech, German, and Swiss markets. The foundry focuses on customers who need specialized parts and need them quickly – for example, machine components for machining and glassworking machines, hydraulic and vacuum equipment, or safety components for various machinery.
The foundry deliberately does not focus on the automotive industry or high-volume production to avoid being dependent on a single segment or supplier.
Situation before implementation: Productivity tracking using Excel, pen and paper
For many years, the foundry used four main tools for preparation and monitoring production: the German production planning system OPTI, Excel, pen and paper.
"We didn't have standardized production, so the output each day largely depended on the goodwill of the employees and the coordination between workstations. And coordinating multiple departments, each led by a different supervisor, was quite difficult," explains Světlík.
Therefore the foundry needed to start monitoring the productivity of machines and workstations.
What were the goals?
Adherence to working hours (ensuring production runs from start to finish).
Elimination of downtime caused by one workstation waiting for another.Improving the efficiency of electric heating in induction furnaces in line with order execution.
Real-time awareness of the number of workers at specific workstations during given shifts.
In other words, improving employee collaboration, implementing modern technologies, and setting standards.
The foundry's leadership was aware of this issue, but it took them a decade to decide to resolve it. While they knew about MES and its application in the automotive industry, they never imagined this type of platform could be used in their type of production.
They believed their expectations were too high: a simple and quick implementation into their operations, followed by straightforward productivity measurement and reporting.
However, after a meeting with SoftLi representatives, they discovered that their fears were unnecessary.
"After receiving the offer from SoftLi, we of course conducted a market research. Acceptable pricing, geographical proximity, personal approach and willingness to accommodate every request were the deciding factors that led us to choose MES SoftLi," adds Světlík.
Implementing MES SoftLi took just a few hours
"The deployment was surprisingly simple. We expected it to be much more complicated. Within a few hours, consultants from SoftLi installed the control units and demonstrated how MES worked directly on our machines. Looking back, we wonder why we didn't make this decision much earlier," admits the foundry's director.
The implementation went smoothly with no issues. In fact, it quickly sparked additional ideas on how MES data could be utilized to completely remove pen and paper from the planning-control-worker flow.
"Tracking productivity through MES SoftLi has opened our eyes to other aspects of production as well," adds the foundry's Světlík.
Implementing MES brought benefits to both company and its employees
Right after implementing the application, the management of the foundry realized that MES SoftLi could solve their performance tracking problem, as they could now clearly and in real-time monitor all the important metrics:
OEE (Overall Equipment Effectiveness)
OOE (Overall Operations Effectiveness)
TUE (Time Utilization Efficiency)
QoW (Quality of Work)
Process Scrap Rate
CT (Cycle Time)
Production
Downtime
MES SoftLi was quickly adopted by the employees as well.
"The motivational component of the remuneration is based on productivity. That's why we used hard data from the MES to show the workers that when they work correctly and follow the basic principles, everyone benefits," explains Světlík.
He is also pleased by the fact that, thanks to the simple interface of MES SoftLi, all employees, regardless of age or education, can use it without any issues.
And what are the results after the implementation?
An increase in the net utilization of workers and machines during working hours.
Improved coordination between workstations, which has eliminated downtime.
A 10% boost in production productivity.
Do you also want to optimise your production?
We help manufacturers of all sizes increase efficiency by up to 20%.
No paper. No downtime. No excuses.
We are the only ones offering a free and instantly available DEMO, as well as the option to test the system on your own machines, without any commitment.